Die casting within Malaysia has become an integral part of Malaysia’s manufacturing and industrial manufacturing industries, playing vital roles in the manufacturing of highly precise metal parts. With the demand worldwide for light, durable, and accurately made metal components is increasing, Malaysia has positioned itself as an important hub for die casting services. This process involves injecting molten metal into dies and molds made of steel under high pressure, resulting in complex shapes with excellent finish and uniformity of dimensional. The method is used extensively in industries such as automotive, electronics, aerospace and consumer goods where performance and precision are essential. Malaysian die casting firms have made considerable investments in the latest equipment, highly skilled labor, and quality assurance processes to meet the standards expected by international clients. Thanks to its location in the middle of Asia with a strong infrastructure and low manufacturing costs Malaysia is a magnet for regional and international businesses in need of reliable die casting solutions.
It is the Malaysian die-casting industry has become renowned by its non-ferrous materials like zinc, aluminum, as well as magnesium. These metals are perfect to create parts that are durable and lightweight. Die casting of aluminum, in particular, is widely practiced because of its outstanding thermal conductivity, resistance to corrosion and weight-to-strength ratio. The properties of aluminum make it particularly popular in the electronics and automotive industries with a high degree of durability and efficacy. are crucial. Zinc die casting, while less common, is used for smaller, more intricate parts that require high precision and a flawless finish. Magnesium die casting is popular for its light weight properties, is increasingly being explored for its potential in reducing the overall weight of vehicles and electronic devices. Its versatility in using various material types allows Malaysian die casting companies to serve a wide range of industries and fulfill a wide range of client requirements.
One of the major advantages Malaysia provides in the die casting field is the increasing pool of skilled techs and engineers well-versed in modern manufacturing techniques. The local universities and institutions have a key role to play in training workers and equipping them with up-to-date knowledge on designing tools, process improvement and quality control. As a result, many Malaysian die casting companies can provide additional services that go beyond casting such as CNC machining as well as surface treatment, assembly and even testing. This value-added approach has allowed Malaysia to be seen not only as a manufacturer of castings in raw form, but as a provider of comprehensive manufacturing solutions. Integration of computer-aided design (CAD) and simulation tools can also help manufacturers reduce mistakes, reduce waste and increase efficiency of production. These advancements have contributed to Malaysia’s high reputation in supplying top-quality, cost-effective components to clients around the world.
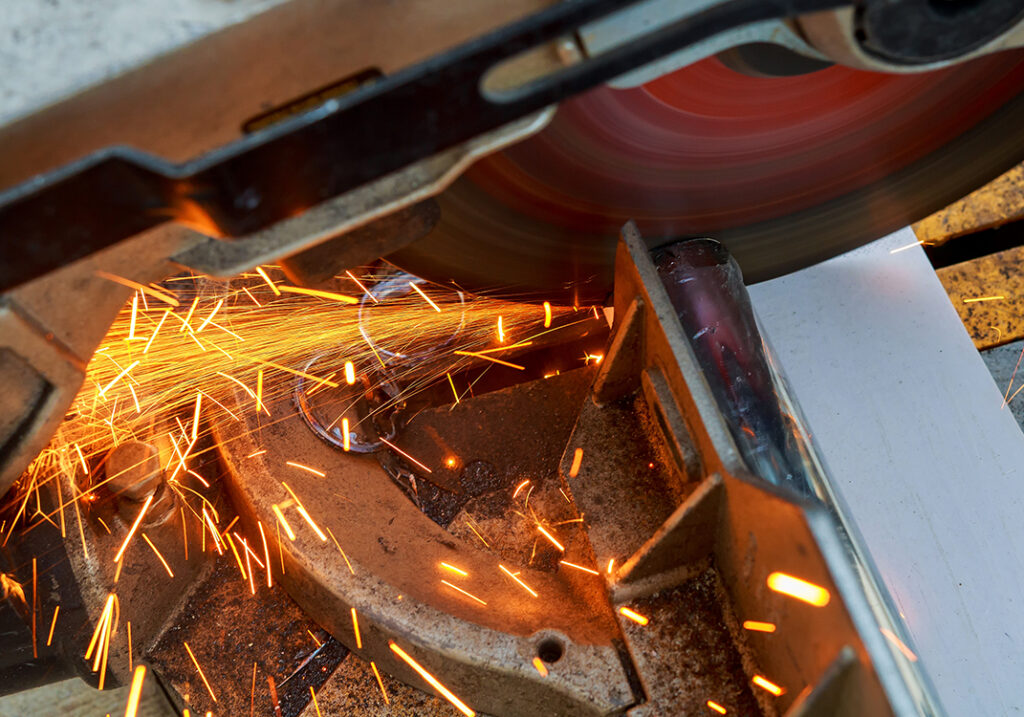
Environmental considerations are also growing more important in Malaysia’s die casting manufacturing. In the midst of global concern for the environment and efficiency of energy, Malaysian manufacturers are adopting more eco-friendly methods. Numerous companies are adopting closed loop recycling, in which scrap metal is reused in the process of production to decrease the amount of waste produced and also to reduce costs for materials. Efforts are also being made to boost energy efficiency making use of electric melting furnaces instead of the traditional gas-fired machines and thereby reduce emissions. Water conservation, proper waste disposal, and compliance with environmental regulations are all an integral part of the overall strategy to ensure that die casting operations are durable over the long run. These practices not only help businesses stay competitive in the global marketplace, but also demonstrate an interest in responsible industrial development. For more information please visit here https://www.senadiecasting.com.my/
Die casting in Malaysia is further strengthened due to its extensive logistics chain and its supply chain. The country’s well-developed infrastructure–including ports, highways, and industrial parks–ensures smooth transportation of materials and finished goods both domestically and for export. Additionally, the proximity of Malaysia to major manufacturing countries across Southeast Asia allows for convenient cooperation and integration into supply chains across the region. The presence of free trade agreements and the government’s aid for investments in manufacturing increase the appeal of the country to companies that run die casting. The companies working in Malaysia enjoy a stable business environment, transparent regulations and easy access to global markets. This makes it an ideal spot to grow die casting capabilities. This interconnected ecosystem supports innovation, speed to market, and scalability–key requirements to compete in the manufacturing industry.
The future for die-casting in Malaysia has a lot of promise because the industry is embracing digital transformation and advanced manufacturing technology. Utilizing Industry 4.0 tools such as automation, IoT (Internet of Things) and data analytics will increase the accuracy of production, decrease downtime, and enhance the predictive nature of maintenance. The collaboration between the private sector as well as government are also being undertaken in order to build smart factories and increase competitiveness. In the face of the constant global demand to electric cars, lighter materials and miniature parts, Malaysian die casting firms have the potential to play a larger part in shaping the future of engineering precision. Die casting’s capacity to adapt in response to changing requirements while maintaining high standards of efficiency and quality assures that die-casting in Malaysia remains a major engine of growth in the economy and technological innovation in the years to come.